by Kenneth SZ Goh
Astill silence hangs over the sprawling ageing room, with rows of about 2,000 whisky casks neatly stacked on top of each other. Rays of sunshine filter in from the doors of the naturally ventilated warehouse that opens up to a surrounding verdant forest. In the casks lie whiskies that have been matured for decades, soaking up the bouquet of fruity and spicy notes from the casks made from American, Spanish, and Mizunara oak.
I am at Yamazaki Distillery in Shimamoto, Osaka Prefecture, which is the oldest single malt distillery in Japan — started in 1923. Armed with a fervent aspiration to develop a whisky suited to the Japanese palate, Suntory’s founder, Shinjiro Torii, famously stated: “I want to create a perfect whisky that reflects the nature of Japan and the spirit of Japanese craftsmanship.”
A century later, this conviction rings true, with the Japanese beverage giant becoming synonymous with its flagship Yamazaki, a single malt whisky that is layered with fruit-forward and Mizunara oak notes.
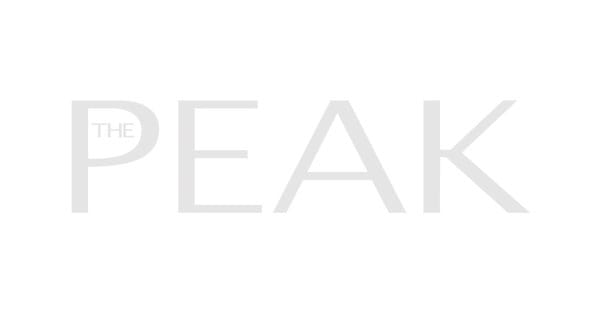
The aging room at Suntory’s Yamazaki Distillery. (Photo: Suntory)
Marking its centennial year of whisky-making, Suntory will roll out four limited edition versions of its iconic whiskies this month. One of them is a special edition of the Yamazaki Mizunara 18, a blend of malt whiskies that are aged for at least 18 years in Mizunara oak casks. The oak enhances the flavour of the whisky by imparting a mellow, spicy flavour and incense-like notes of sandalwood and agarwood.
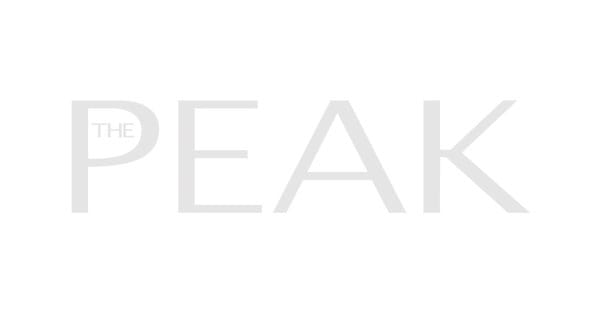
The 100th anniversary edition of Yamazaki 12 and 18 Years Old. (Photo: Suntory)
Chronicling Suntory’s whisky-making journey is an exhibition that will be held at the ArtScience Museum from July 13 to 17. Visitors can watch an anniversary film by American filmmaker Sofia Coppola, who directed the 2003 film Lost in Translation, which propelled the whisky to global fame. The exhibition will also cover Japanese bar culture and have an immersive bar space where visitors can savour the whiskies.
Refining craftsmanship
Celebrations aside, Suntory is zeroing in on the whisky-making processes before the liquid gold is matured in casks. It will invest 10 billion yen (S$97 million) to renovate its Yamazaki and Hakushu distilleries over the next two years. The latter mainly produces Hakushu, a single malt whisky that has a light, fruity, and slightly smoky taste. Both distilleries, which also conduct popular visitor tours, are closed for renovation until early next year.
When the two distilleries re-open, they will practice floor malting, the traditional method of spreading out barley — the main ingredient in whisky — on the floor to kickstart the germination process that produces sugar, which is later fermented into alcohol.
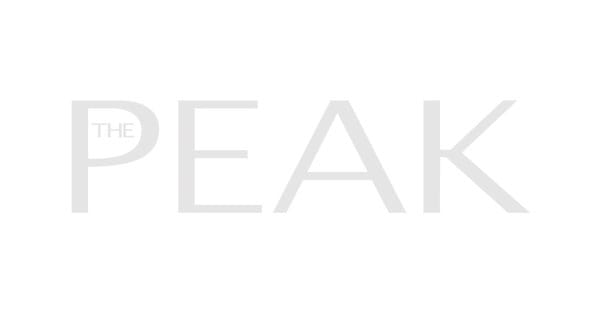
Shinji Fukuyo, chief blender of the House of Suntory. (Photo: Suntory)
Shinji Fukuyo, the fifth-generation chief blender of the house of Suntory says: “Floor malting helps to further improve the quality of whisky, as research has shown that using malt that has undergone the process improves the ageing and flavour quality of whisky. This also enables us to realise various malting conditions with the traditional method.”
Another new initiative is the use of electric-powered pot stills in Yamazaki’s pilot distillery, which is used for research and development. Traditionally, direct-heating copper pot stills are where the alcohol undergoes multiple rounds of distillation to become whisky.
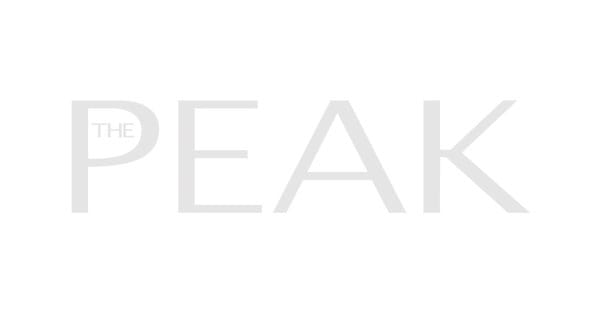
Copper stills made in Japan and Scotland. (Photo: Suntory)
While research on the impact of the whisky’s quality is still being carried out, Fukuyo elaborates: “With electric-powered pot stills, carbon dioxide emissions from the distillery can be reduced, lowering the environmental impact. The heating control can be adjusted more precisely, so thermal efficiency is higher.”
“If there is a chance to improve the quality of whiskies, we are willing to take on challenges through new technology and traditional processes,” he affirms.
Meeting an insatiable demand for whisky
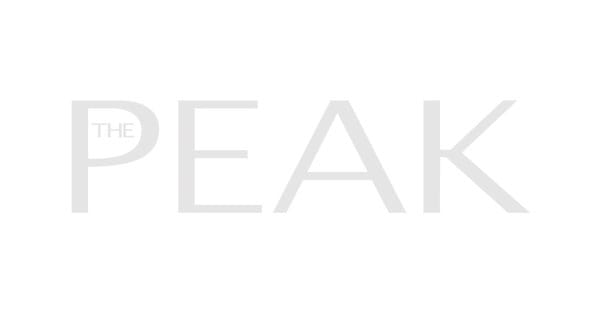
Shinji Fukuyo, chief blender of the House of Suntory. (Photo: Suntory)
Touring Yamazaki Distillery opened my eyes to the labour-intensive whisky production process. Barley, which is imported from Scotland, is ground and mashed, converting starch into sugar, and filtered to become wort. This process fills the warm room with a sweet, malty aroma.
The wort is then fermented in five-metre-tall wooden and stainless steel tanks, called washbacks, before being distilled in copper stills from Scotland and Japan. Capping off the production process is the maturation stage, where the whiskies are left to rest in casks.
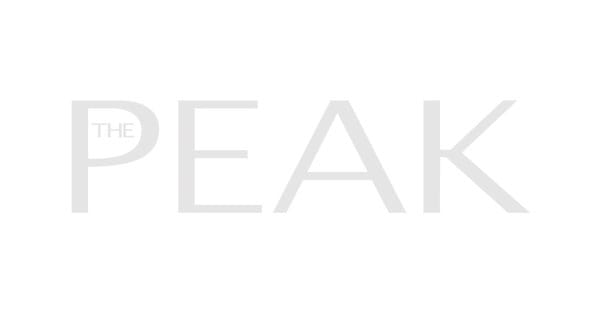
Photo: Suntory
While the whiskies are maturing in blissful silence, there has been much buzz over the escalating prices of the Yamazaki whiskies. According to auction house Sotheby’s, a 50-year-old Yamazaki (which was first released in 2005) was sold for a whopping US$400,000 (S$538,000) in 2019. The price hike is a result of an insatiable demand that outstripped supply after Suntory embarked on a wildly successful marketing campaign in 2008 to promote highball — a concoction of whisky and carbonated water. That also sparked a culture of having highballs with meals, especially at izakayas, among younger consumers.
Demand also continued to spike with a slate of wins for Yamazaki whiskies at international competitions. One note-worthy win was the Yamazaki 12 Years Old receiving a Gold award at the International Spirits Challenge in 2003, which also paved the way of greater recognition for its sister brands such as Hibiki and Hakushu.
Apologising for the shortfall in whisky supply, Fukuyo reassures: “Since around 2010, we have been working to reinforce our supply system by making capital expenditures in facilities and making scheduled shipments so that we can continue to provide our products in the future.”
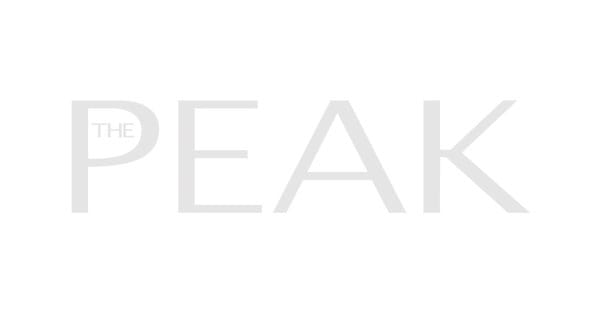
Suntory’s Yamazaki Distillery turns 100 this year. (Photo: Suntory)
He explains: “Whisky production is limited by the long maturation period. With demand surpassing supply, we cannot increase shipments overnight, and shortages of certain products are continuing.” He reveals that Suntory has increased the production of its whiskies by over 50 per cent, in terms of production capacity at the end of last year as compared to 2016.
Since around 2010, we have been working to reinforce our supply system by making capital expenditures in facilities and making scheduled shipments so that we can continue to provide our products in the future.
– THE HOUSE OF SUNTORY’S CHIEF BLENDER SHINJI FUKUYO
On creating whisky expressions, Fukuyo, who counts the award-winning Yamazaki 1984 as one of the most memorable whiskies that he has crafted, says: “It is important to have a vision for the future in terms of knowing the types of whiskies that consumers will enjoy given that whisky takes such a long time to mature. What we are preparing now will only be ready up to 30 years later.”
Label of love
Washi artist Eriko Horiki shares the story behind creating whisky labels.
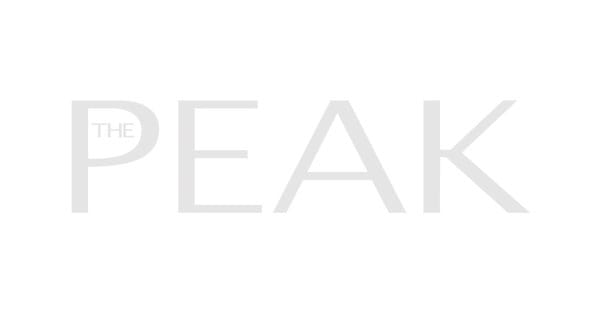
Suntory’s Hibiki blended whisky. (Photo: Suntory)
Labels are often a second thought next to attention-grabbing whisky bottles and cases. But washi artist Eriko Horiki, who has been producing labels made with traditional Japanese paper for Suntory’s Hibiki blended whisky range since it was launched in 1989, thinks otherwise.
“A whisky takes many years to develop a deep flavour,” says the Kyoto-based artist. “It is important that the label is the face of the product, as it represents the farmers and blenders who have worked on it.”
The label plastered on each exquisitely-crafted Hibiki bottle, which has 24 facets that represent the number of seasons in the Japanese lunar calendar, is made with echizen washi paper. It is made with the traditional technique of crafting thick layers of paper precisely, and designs are created by juxtaposing multiple layers of paper.
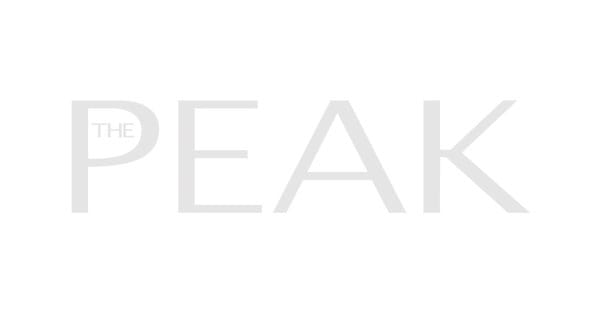
Washi artist Eriko Horiki. (Photo: Suntory)
At 24, Hiroki left a stable job at a bank to start a washi company. The self-taught artist is pushing the boundaries of washi with a diverse range of products that include wall and ceiling screens and lamp shades.
Injecting a fresh dose of innovation into the time-honoured art, she incorporates the effects of natural sunlight into her washi designs to “portray a transition of seasons”. Similarly, she applies this technique to producing whisky labels. She explains: “I consider where the whisky bottles are placed and the amount of light they would get. The label’s lighting effect also depends on how much whisky is left in the bottle. I hope that consumers can imagine the flavour and aroma of the whisky by looking at the labels.”