by Allyson Klass
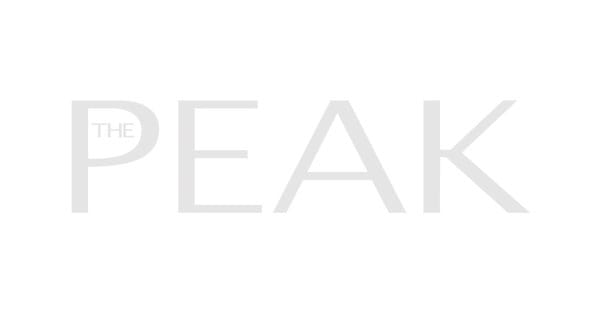
Photo: Rolex
Creating a Rolex dial is a unique alchemy combining traditional craftsmanship and state-of-the-art processes. It takes at least 60 operations to transform a metal disc, called a blank, into a beautifully embellished masterpiece that imbues each watch with its soul and distinctive character.
This element is so important that some 500 specialists — mechanics, gem-setters, electroplaters, and dial printers, among others — work exclusively on dial-making at the manufacture’s dedicated site in the Chêne-Bourg district of Geneva. This strategic approach allows Rolex to expand its colour palette continually, adding new shades and nuances each year.
Each dial is a miniature artwork, where hues, reflections, and texture combine harmoniously with decorative elements to create the timepiece’s unique personality. Typically made from brass, Rolex dials are often enhanced with precious metals such as yellow, white, or pink gold.
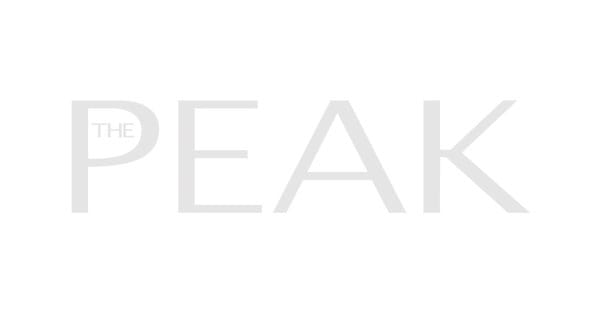
Dials in decorative stone eisenkiesel and onyx for the Day-Date 40 and turquoise for the Day-Date 36. (Photo: Rolex)
They may also feature natural materials, including mother-of-pearl or decorative stones like eisenkiesel, opal, green aventurine, carnelian, or turquoise. Here, Rolex’s expertise in cutting discs from raw materials shines. Only samples that meet its stringent aesthetic standards are selected to become stunning statement-making dials.
The manufacture employs three main techniques to colour its dials. The first is lacquering, which produces a wide array of opaque hues and remains the go-to method for achieving pristine white dials and black versions seen on the Submariner.
Next, electroplating combines various metals to achieve metallic colours like silver, champagne, slate, and steel. This complex process can also create striking black dials.
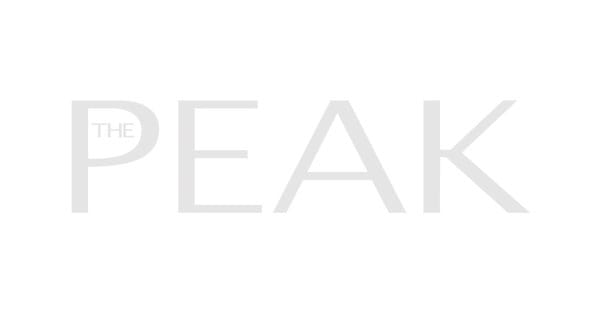
Testing for the right shade of lacquer according to the sketches created by Rolex’s Design Department. (Photo: Rolex)
Lastly, physical vapour deposition (PVD) involves applying ultra-thin layers of metal and metal oxides to the dial’s brass base in a vacuum chamber. This sophisticated method adds intense hues to metallic finishes while expanding the electroplating spectrum to include luxurious tones such as olive green, chocolate, bright blue, pink, ice blue, and dark grey.
Also mastered in-house is the age-old technique of grand feu enamelling, renowned for producing vibrant and intense shades that can stand the test of time. The exclusive puzzle motif dials on the 2023 Day-Date 36 are a prime example of this intricate hand-craft.
This ancestral method is also used for exquisite hour markers on some diamond-paved dials.
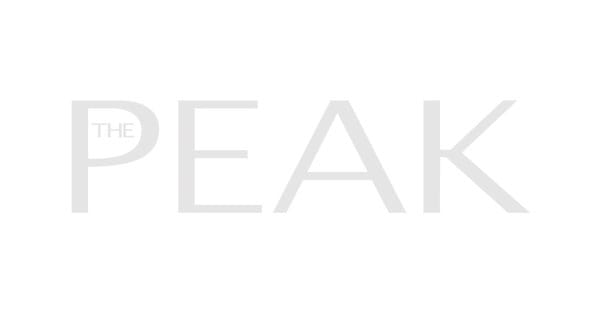
Dial with motif made using the champleve method of grand feu enamelling for the Day-Date 36. (Photo: Rolex)
Rolex dial colours result from extensive research and exceptional skills that often evolve with changing times. Take, for instance, the iconic Rolex champagne-coloured dial, which evolved multiple times in the 1980s and 1990s when it gained warmth and pinkness. Ice blue, a shade reserved for 950 platinum models, has also varied over the years.
Final surface finishing transforms the dial’s appearance and texture. A simple black dial can look sporty with a matte finish or refined with a glossy varnish. Despite advanced technology, the human eye is the final judge of a new tint. While laboratory equipment can measure thousands of shades, real beauty is ultimately judged by the discerning eyes of Rolex’s in-house dial specialists.