by Christy Yoong
In 1853, having outgrown its original location in Geneva’s Quai des Bergues, Patek Philippe moved across to the left bank of the Rhône, setting up a new Salon and manufacture in a building in front of the Port du Commerce. It was, at that time, a counterintuitive move as the left bank was an unfashionable part of the city and hardly the place for a watchmaker of Patek Philippe’s calibre and ambition.
Time, however, has vindicated that decision. From here on the rue du Rhône, Patek Philippe would continue its inexorable climb to horological eminence, committing to its patrimony yet pushing boundaries where it can. The building was the first in the area to heated and electrified. It even supplied electricity to a nearby hotel.
This rue du Rhône space, extensively expanded and refurbished, remains in the watchmaker’s hands, serving as one of Patek Philippe’s sumptuously decorated Salons (there are only three Patek Philippe’s Salon worldwide; the other two are in London and Paris) on the ground floor. Minor repairs on timepieces are carried out on the first floor, while offices occupy the rest of the space. Manufacturing, however, on moved on.
The Big Pictures
Patek Philippe today is much the same company compared with the one that moved to rue du Rhône in 1853 except for one crucial detail – it is vastly much larger in scale. It has 3,000 employees worldwide, two-thirds of whom are in Geneva. It produces around 70,000 watches a year, 63,000 of which are mechanical pieces. Its catalogues list 17 basic calibers, more than 50 movements references and 150 watch references.
The watchmaker operates 400 state-of-the-art precision and production machines, producing 10,000 different components. Creating those 70,000 timepieces requires 16,500,000 components, all of them made in the current centre of the Patek Philippe universe, Plan-les-Ouates, just outside of the city of Geneva.
Patek Philippe moved to Plan-les-Ouates in 1996, becoming the first watch manufacturer to establish a presence in this Genevan suburb community that is now referred to as ‘Plan-les- Watches’. This pioneering move reunited the brand’s individual activities that were previously scattered over a dozen sites throughout Geneva. This space, however, would prove too small to cope with the manufacture’s growth, leading to some operations being relocated to the neighbouring community of Perly in 2003.
While this solved the problem, it wasn’t the ideal situation for what is now Geneva’s last family-owned independent watch manufacturer. An existing office building was converted into an atelier complex, where all movement components were eventually produced, but a more permanent solution was required to surmount the problem of space and, more importantly, secure the long-term independence of the company.
PP6
PP6, as the building is named, is more than merely Patek Philippe’s production centre. It is also a statement of intent and ambition. Inside those gleaming white walls is a reaffirmation of all the values that the brand holds dear – a commitment to quality and craft, a dedication to the skills and expertise that are the pillars that underpin each and every timepiece that bear the Patek Philippe Seal.
This CHF600 million construction – CHF500 million for the building and the remainder for interiors and equipment – is an edifice of superlatives.
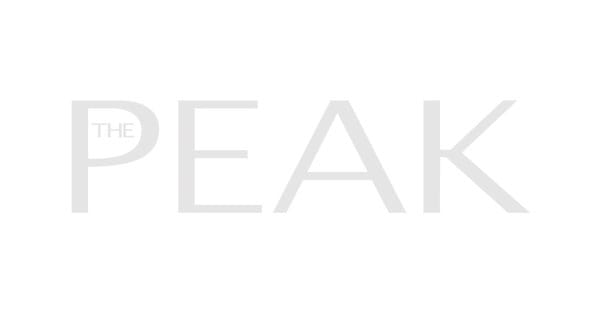
Room, ambiance, description et détails
From the outside, it looks stately, like an ocean liner just waiting to cast off. Large-format glazing – abundant daylight is the watchmaker’s delight – interacts with white concrete passageways along the entire façade and the intermittent bronze-coloured fire escapes. And, as with the intricate timepieces that Patek Philippe creates, details make a difference: the slight horizontal curvature of the passageways is reminiscent of the gently rounded octagon of the Nautilus case, while the balustrades of the fire escape ladders have silhouettes that resemble the form of leaf-shaped hands.
Under One Roof
Inside, corridors are cavernous enough that comfortable walking shoes are a necessity. Banks of elevators – there are a total of 20 for passengers and freight – hum efficiently and while there is constant movement, there is no sense of a rush. There is, in fact, a slightly reverent hush in the air, the very atmosphere seemingly to acknowledge that serious work is taking place here.
In that sense, bringing all the relevant crafts and production ateliers together is merely an exercise in rationalisation, an agglomeration of Patek Philippe’s complete repository of horological know-how under one roof and promote efficiency. The ground and first floors of PP6, for example, are reserved for production and manual finishing of movement parts, including plates, bridges, wheels and form parts. On the second floor is the machining, manual polishing and assembly of exterior parts like cases and bracelets, and gem-setting. The production of spare parts needed by Customer Service and the restoration of antique timepieces also take place here.
On the third floor, you’ll find further production-related departments such as Research & Development in the fields of new materials and new technologies (Patek Philippe Advanced Research), an Haute Horlogerie department and a new unit for prototyping operations. The fourth floor provides space for further evolving and transferring of the Rare Handcrafts skills, like manual engraving, enamelling, guilloching, wood micromarquetry, that Patek Philippe has actively promoted. Here, too, is an auditorium that seats 299 persons as well as training rooms for watchmakers and members of the international sales network.
In those ateliers, those aforementioned 400 state-of-the-art precision and production machines purr industrially, producing components, some measured in mere millimetres, that still require finishing by hand. Microscopes and hand tools have their roles as well. Gem-setting demands intricate adjustments that call for steady hands and finer judgement calls. There are 15 different steps to assembling the bracelet for the Nautilus, while its case requires 40 separate actions. Modern technology sits comfortably beside centuries-old techniques. It takes a lot of parts and skills before a Patek Philippe watch starts beating.
Eye On The Future
On the top floor of PP6 is a penthouse restaurant for 880 guests as well as four VIP lounges. There is, also, a panoramic view of the landscape – France, you’ll soon realise, isn’t that far away – and the nearby mountains. From this height, the future seems bright and clear for Patek Philippe.
PP6, ultimately, has one goal, which Patek Philippe has continuously embraced – the creation of the world’s finest timepieces.